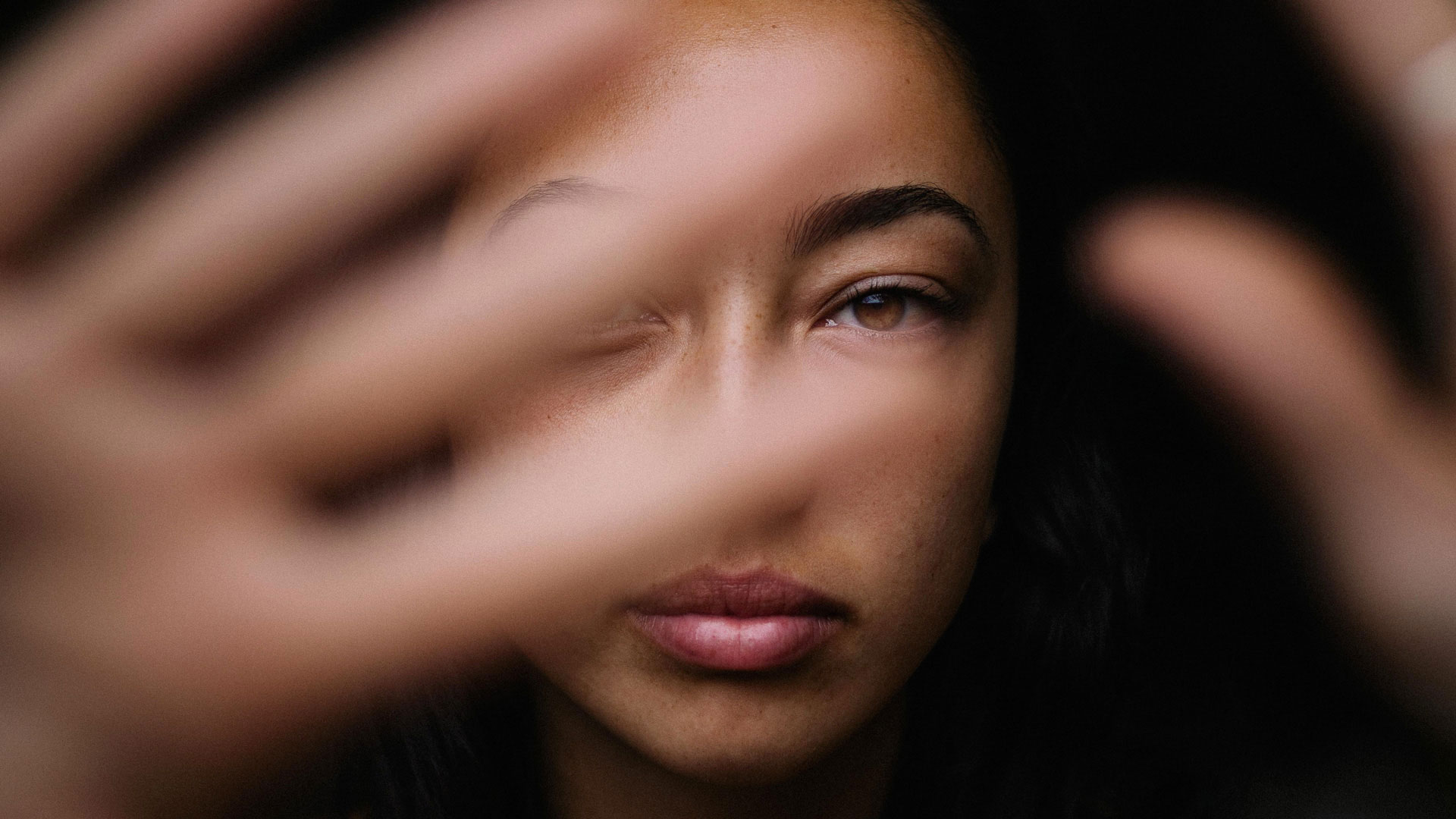
Fossil freedom is just around the corner!
Thanks to our fossil-free steel and our new scrap-based steel made without fossil carbon emissions, we are paving the way for a greener future.
Learn moreThanks to our fossil-free steel and our new scrap-based steel made without fossil carbon emissions, we are paving the way for a greener future.
Learn moreSSAB’s breakthrough fossil-free technology is the first true steelmaking transformation for centuries. Our customers around the world will get premium high-strength steel, adapted to the future.
SSAB’s annual general meeting (AGM) was held today, April 24, 2024, in Stockholm. The shareholders were also able to exercise their voting rights by postal voting. The AGM resolved on a dividend of SEK 5 per share.
The first quarter · Revenue was SEK 27,148 (31,904) million · Operating result was SEK 3,157 (4,733) million · Earnings per share were SEK 2.57 (3.59) · Net cash was SEK 18.2 (15.6) billion · Investment decision of EUR 4.5 billion for fossil-free steel mill in Luleå
The second phase of the joint project FOSSA (Fossil-free Steel Applications) coordinated by SSAB Europe has received a positive financing decision from Business Finland. The project supports SSAB’s goal of building a fossil-free value chain from steel production to the end customer.
SSAB is a specialized steel manufacturer. We only make steel grades with qualities that are fine-tuned to make applications stronger, lighter, safer, easier to produce, more long-lasting, fuel efficient and sustainable – all depending on what’s highest on the users’ list of priorities.
The place to go for corporate, financial, product or technical information.
Keep up-to-date on the latest product, design and manufacturing news.
Search for our products, steel grades and standards
We’re here to provide you with everything from innovative steel solutions to manufacturing resources and hands-on workshop assistance. Welcome to Services if you’re looking for pre-fabricated steel parts, wear parts and engineering services. Or turn to Support for design considerations, choice of steel grades, production technologies and much more. We look forward to hearing from you.
SSAB has a strong position as a specialized manufacturer for the high-end steel market. Our financial target is to reach industry-leading profitability, benchmarked against a number of other major steel companies.
At SSAB, there are many job opportunities in steel manufacturing, finance, research, environmental issues, marketing, business development and HR. If you are ready to move onwards and upwards, contact us.
We want to become the first fossil-free steel company in the world. Our vision is at the core of our entire operation. We are striving to create a stronger, lighter and more sustainable world. Sustainability is a key business driver for both us and our customers.