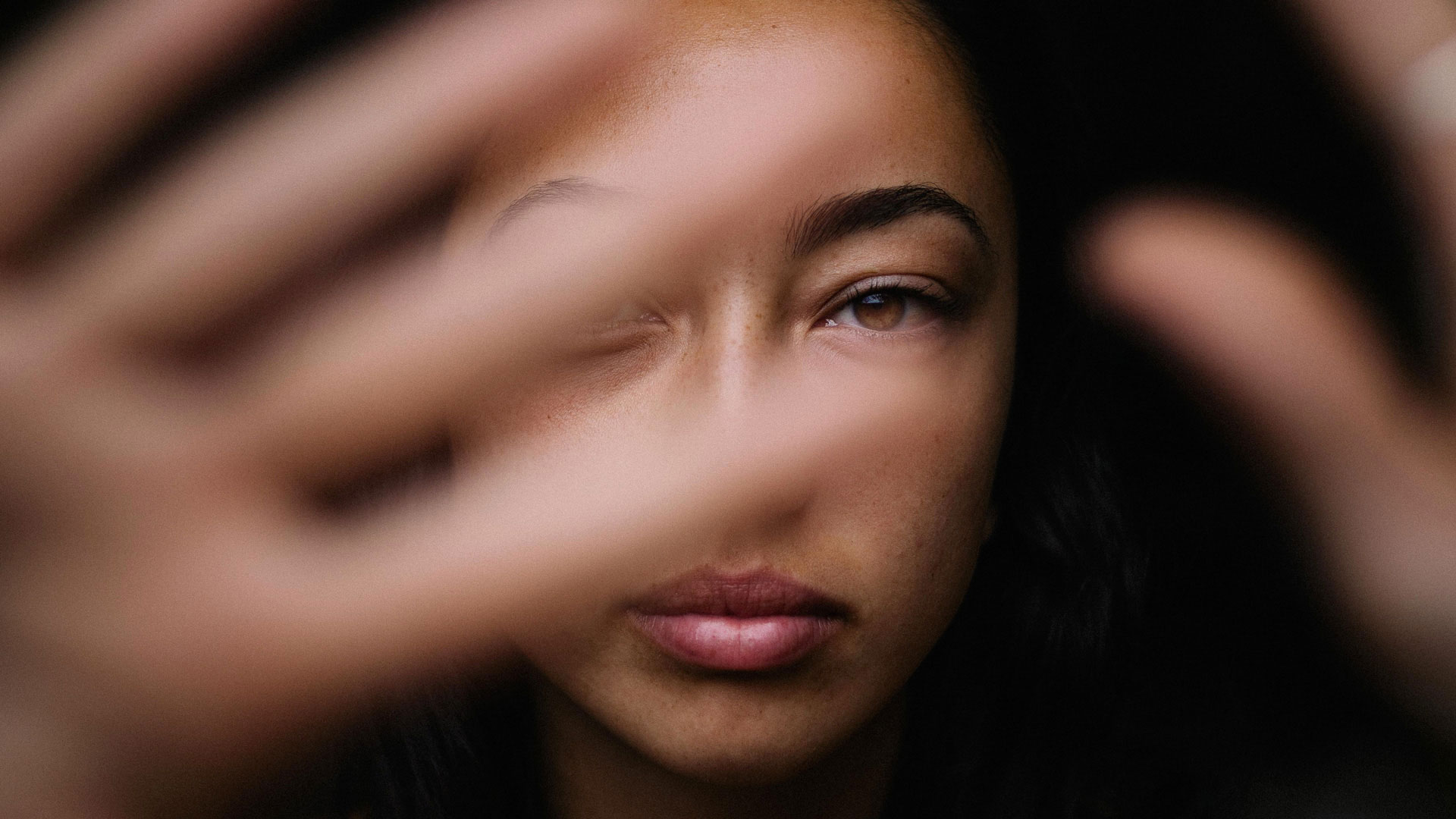
スティール の 未来を刷新
SSABが現在開発中の画期的な化石燃料フリーテクノロジーは、製鉄産業に真の変革をもたらします。 SSABの世界中の顧客は今まで通り高品質 かつ高強度 の鋼板を入手できます。 未来に適応する力が加わります。
詳しく読むSSABが現在開発中の画期的な化石燃料フリーテクノロジーは、製鉄産業に真の変革をもたらします。 SSABの世界中の顧客は今まで通り高品質 かつ高強度 の鋼板を入手できます。 未来に適応する力が加わります。
詳しく読むSSABは特殊鋼メーカーです。 強度、軽量性、安全性、作りやすさ、耐用性、燃料効率、持続可能性など、お客様が最も重視する要素に合わせて製品性能を最適化した特殊鋼を専門に製造しています。
企業情報、財務情報、製品情報、技術情報をこちらでご覧いただけます。
製品、鋼種、規格を検索
高温での耐用年数向上を実現するHardox HiTemp耐摩耗鋼板